11/06/26 |
a.jpg) |
|
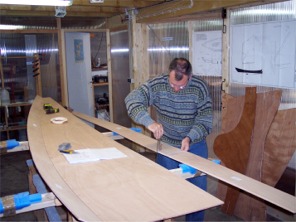 |
|
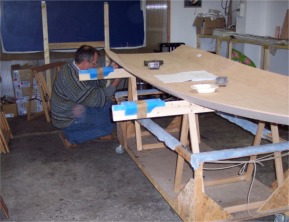 |
|
|
Cliquez sur les photos pour les voir en grand |
|
|
Le week-end dernier (18 et 19 juin), je suis allé participer à la Route du Sable, rassemblement de voile-aviron en mémoire des anciens sabliers qui venaient jadis livrer dans les terres le maerl (sable grossier constitué par les débris d'une algue à squelette calcaire, qui servait à amender les terres trop acides afin d'améliorer leur rendement). L'itinéraire de la Route du Sable remonte la partie maritime de l'Aulne (en aval de Chateaulin où commence le canal de Nantes à Brest). Voir notre page consacrée à la Route du Sable 2011. |
|
Aussitôt de retour à l'atelier, je reprends avec Gilles la construction accompagnée de son PassageMaker (numéro 34), déjà préparée sur deux matinées avec lui. Gilles a cousu le bordé 1 bâbord sur la sole et il trace ici l'écartement pour les futurs trous des sutures qui vont relier le bordé 1 tribord à la sole. |
|
Gilles noue l'une des dernières sutures reliant le bordé 1 tribord à la sole. |
|
|
|
|
|
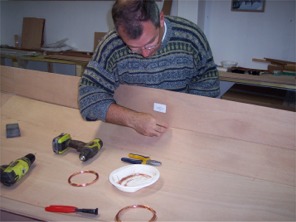 |
|
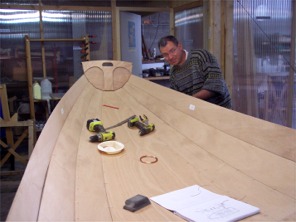 |
|
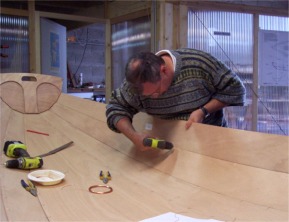 |
|
|
|
|
|
Gilles enchaîne avec le bordé 2 tribord. Nous avons préalablement percé les trous le long du bord haut du bordé 1, il s'agit de percer le bordé 2 en regard de chaque trou de suture dans le bordé 1, puis de passer une suture en fil de cuivre dans chaque trou, afin de lier les bordés entre eux, puis de les coller. |
|
Bordé 3 tribord : nous venons d'insérer la marotte et le tableau entre les extrémités de la sole et des bordés 1 et 2. Pour chaque nouveau bordé, nous commençons par percer et nouer trois sutures pour le tenir en place : une à l'avant, près de la marotte, une au milieu et une à l'arrière près du tableau. |
|
Gilles perce le bordé 3 tribord en regard d'un trou sur le bord haut du bordé 2. |
|
|
|
|
|
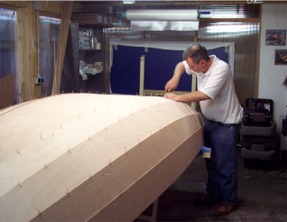 |
|
| |
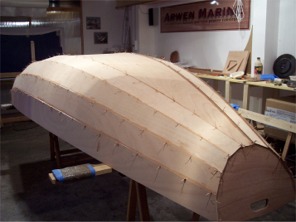 |
|
|
Cliquez sur les photos pour les voir en grand |
|
|
Nous avons fini de suturer tous les bordés ainsi que la structure transversale (une membrure centrale et deux cloisons pour les compartiments étanches avant et arrière), puis nous avons retourné la coque et Gilles est maintenant occupé à resserrer toutes les sutures. En effet, les "jours" entre les bordés sont maintenant fermés du fait que la coque à l'envers pousse les bordés en compression les uns contre les autres. |
|
Premier collage : Gilles est ici occupé à racler l'excédent d'époxy chargée que nous avons déposée dans tous les joints à la seringue, puis lissée à la cuiller, selon une technique ancestrale que j'ai découverte en 2008. |
|
Et voilà : au terme de notre première journée de travail (si l'on ignore les deux demi-journées de préparation des pièces), le bateau est cousu et collé. C'est presque fini, quoi ! |
|
|
|
|
|
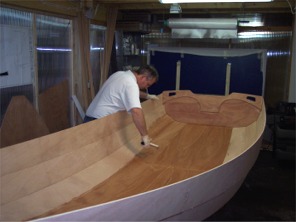 |
|
|
|
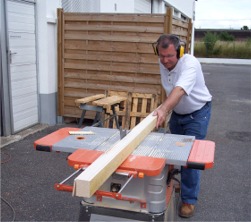 |
|
|
|
|
|
Le lendemain, Gilles passe au rouleau une couche d'imprégnation à l'époxy "claire" sur toute la surface intérieure, après avoir coupé puis extrait toutes les sutures en fil de cuivre. |
|
Dans la foulée de la couche d'imprégnation, nous déposons un filet d'époxy chargée dans tous les joints intérieurs. Tous ces joints sont lissés à la cuiller, puis nous nettoyons l'excédent d'époxy chargée chassée hors des joints lors du lissage, c'est ce que Gilles fait sur cette image. |
|
Pendant que l'époxy durcit, nous commençons le travail sur les espars. Sur cette image, Gilles utilise la scie de table pour faire une coupe sur une face du mât afin d'affiner sa partie haute. |
|
|
|
|
|
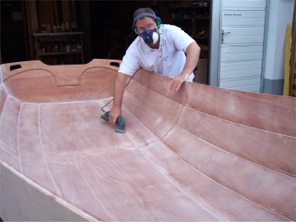 |
|
|
|
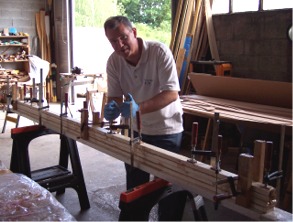 |
|
|
Cliquez sur les photos pour les voir en grand |
|
|
Après 24 heures, il est temps de poncer la couche d'imprégnation sur l'intérieur de la coque. Gilles est d'accord avec moi que ce n'est pas la partie la plus intéressante de la construction navale... Malheureusement, c'en est phase importante et récurrente... Il a utilisé successivement la ponceuse orbitale (ou excentrique), la ponceuse vibrante, puis la ponceuse delta, visible sur cette image, et enfin la cale à poncer à l'huile de coude. |
|
Après le ponçage, nous passons à la stratification du fond de la coque, sur l'intérieur. Voici la photo que j'aime bien vous montrer, avec le tissu de verre partiellement saturé d'époxy. Je ne me lasse pas de m'émerveiller de la façon dont le tissu disparait quand il est mouillé d'époxy... |
|
A défaut de bois d'épaisseur suffisante "propre" (sans trop de noeuds), nous collons deux plis de 23 mm d'épaisseur pour faire la bôme et la vergue de la voile au tiers prévue pour le PassageMaker de Gilles. |
|
|
|
|
|
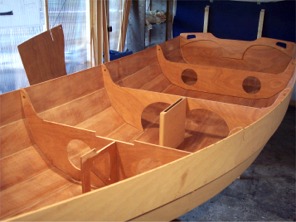 |
|
|
|
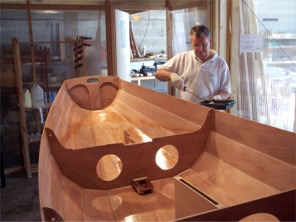 |
|
|
|
|
|
Jour 5 : nous avons re-suturé les cloisons et la membrure centrale en place, et ajouté l'épontille de mât, qui n'aura pas ce rôle car nous n'installons pas le gréement standard de sloup houari : le mât non haubanné sera emplanté juste en arrière de la cloison avant. On voit d'ailleurs que l'épontille et la cloison sont entaillées pour laisser place au renfort d'étambrai, qui sera collé sous le pontage avant. |
|
Cette image au cadrage audacieux (et hautement artistique) prise par la découpe de la trappe tribord du compartiment arrière montre le pied de mât au pied de la cloison avant, visible à travers l'allègement de la membrure centrale. Il est juste monté "à sec", sans époxy, de même que l'ensemble de la structure interne et le puits de dérive. On voit d'ailleurs un peu de jour autour de la membrure centrale. Nous allons maintenant démonter le pied de mât et le puits de dérive, les encoller et les remonter, puis nous ferons tous les joints-congés qui tiendront la structure. |
|
Gilles passe une couche d'époxy claire sur l'ensemble de la surface intérieure du caisson avant, dont nous allons maintenant coller le pontage, également fraîchement revêtu d'une nouvelle couche d'époxy. |
|
|
|
|
|
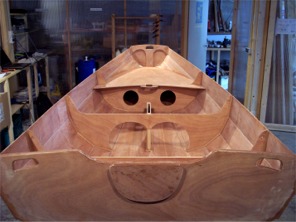 |
|
|
|
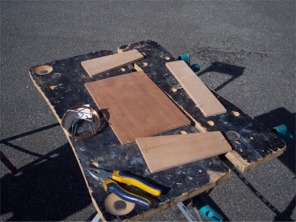 |
|
|
Cliquez sur les photos pour les voir en grand |
|
|
L'aspect "stéréo" de ces trappes jumelles ne nous a pas arrêtés. Il est en effet impossible de n'installer qu'une trappe centrale sur ce PassageMaker, du fait de la présence du mât lorsque le bateau est gréé. De plus, la largeur importante de ce caisson rend les deux trappes bien pratiques pour en extraire les objets qui y seront abrités. |
|
Trappes stéréo également à l'arrière, du fait de la présence future d'une batterie de moteur électrique au centre du caisson, juste contre la cloison : les deux trappes sont une obligation afin de pouvoir utiliser indépendamment les deux parties latérales de l'hénaurme caisson arrière. |
|
Nous avons décidé d'utiliser la technique du cousu-collé pour construire le "bac à batterie" que nous allons installer dans le coqueron arrière. |
|
|
|
|
|
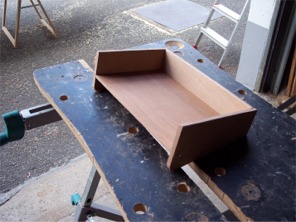 |
|
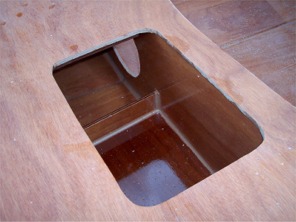 |
|
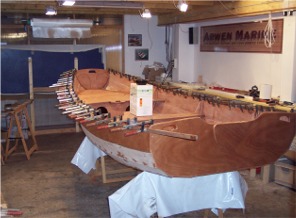 |
|
|
|
|
|
Voici le bac à baterie cousu : plus qu'à le coller ! |
|
Le bac collé et installé dans le compartiment arrière, vu à travers la découpe de la future trappe qui permettra d'y déposer la baterie, ce qui fait trois trappes pour le compartiment arrière. |
|
Collage des dessus de caissons et du banc central, ainsi que du premier pli des listons. |
|
|
|
|
|
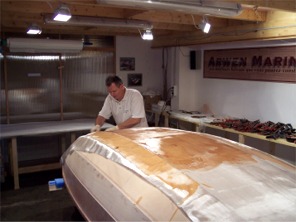 |
|
|
|
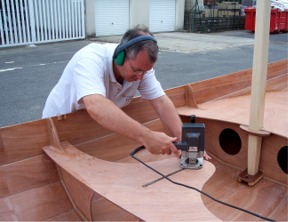 |
|
|
Cliquez sur les photos pour les voir en grand |
|
|
Nous avons retourné la coque afin de faire une seconde couche sur les joints, intouchés depuis le premier collage, et nous faisons ensuite la stratification sur l'extérieur de la coque. Comme sur l'intérieur, la stratification est limitée à la sole et à la première paire de bordés. |
|
Après durcissement partiel de l'époxy sur la stratification, Gilles passe une seconde couche d'époxy pour rempir la trame du tissu de verre, et pour constituer la première couche d'imprégnation sur le reste de l'extérieur de la coque. |
|
Gilles ouvre le haut du puits de dérive à la défonceuse, devenue son outil favori, avec une fraise droite à guide : nous avions préalablement scié une pré-découpe plus étroite que l'ouverture à pratiquer. |
|
|
|
|
|
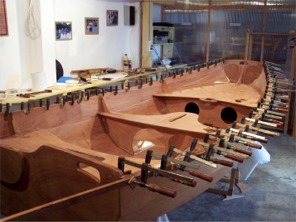 |
|
|
|
 |
|
|
|
|
|
Et collage du second pli des listons, samedi soir, au terme de nos six jours de construction (plus deux demi-journées de préparation). Il reste à finaliser les listons, faire les joints sous les sièges et faire une dernière couche d'époxy sur l'ensemble de la surface intérieure et extérieure. |
|
Je viens aussi de commencer la construction d'un Oxford Shell, un skiff d'aviron pur (6.25 m de longueur pour 56 centimètres de large), mais je vous en dirai plus dans ma prochaine mise à jour. |
|
Hervé nous envoie les 4 photos suivantes de sa Yole de Chester, enfin finie et prête à prendre la mer. |
|
|
|
|
|
 |
|
|
|
 |
|
|
Cliquez sur les photos pour les voir en grand |
|
|
"Prendre la mer" était un peu rapide : Hervé effectue un test de flottabilité en piscine. |
|
Le plan d'eau est un peu limité pour évoluer à l'aviron... |
|
Poursuite du test de flottabilité, avec 4 personnes à bord. La Yole est déclarée en catégorie D pour 3 personnes seulement, mais on voit qu'elle en porterait 4 sans peine (sauf pour le nageur peut-être)... |
|
|
|
|
|
|
|
|
|
|
|
|
|
|
|
|
|
Claude m'envoie une sélection de photos de la Semaine du Golfe que j'ai ajoutées sur la page dédiée à cet évênement. |
|
|
|
|
|
|
|